With the development of science and technology, people have put forward various new requirements for the surface performance and appearance of CNC machining of aluminum alloy shells. For example, when electroplating is used in large areas of CNC machining products of aluminum alloy shells, people increasingly hate the luminous electroplating luster. , Turning to love smoke-like tones, as well as satin-like elegant tones. Therefore, electroplating alloys were developed. Here is a brief introduction of several decorative electroplating alloys used in product finishes.
1. CNC machining of aluminum alloy shell and electroplating tin-cobalt alloy
The tin-cobalt alloy electroplating and cobalt electroplating have similar colors, but they are softer and more popular. At present, most foreign countries are used to replace chromium. Cobalt electroplating is not easy to barrel plating, while electroplating tin-cobalt alloy is suitable for barrel plating of small parts. In addition, electroplating tin-cobalt alloy has excellent throwing ability and barrel plating ability, so it can be applied to workpieces with complex shapes. If double-layer nickel is electroplated on the bottom layer, its corrosion resistance is no less than that of electroplated chromium. In order to prevent the surface from discoloring, it should be treated by immersion in chromate, which can also improve its corrosion resistance.
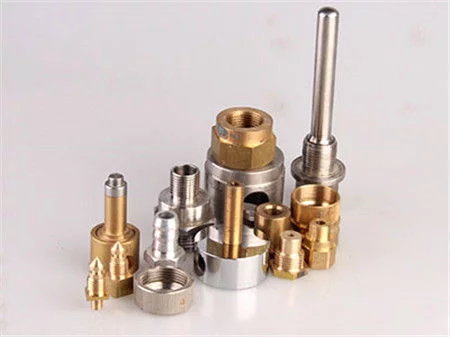
Its appearance is a pale rose hue, which makes people feel very good, and has excellent corrosion resistance. If tin-nickel alloy electroplating is applied to a shiny substrate or on a bright nickel plating layer, a good shiny surface can be obtained. If electroplating is performed on a matte surface (pear pattern), the original condition of the surface can appear. The plating ability of the electroplating layer is very excellent, almost no leveling effect, so it is suitable for the electroplating of very fine lines and rotating processed products.
2. Aluminum alloy CNC machining electroplating copper-tin alloy
The color of the low-tin bronze coating of the aluminum alloy shell is pink or golden, with fine crystals. It has high corrosion resistance and good polishing performance. It is often used as a protective-decorative nickel underlayer and is used in light industry and handicrafts. , Mechanical instrument industry and other industries. The color of the medium tin bronze coating is golden, and the corrosion resistance is good. Mainly used as the bottom layer of decorative chrome plating. The hardness and air stability of aluminum alloy processing are higher than that of low tin bronze plating. However, due to the high tin content of the plating layer, the bottom layer of the protective decorative plating layer is prone to blooming after being coated with chromium. This is the weakness of the medium tin bronze plating layer. The high tin bronze coating has beautiful silver-white luster and good polishing performance, high hardness and wear resistance. It is used in industrial design to replace silver or chromium as protection for reflective equipment, instruments, daily commodities, etc. Decorative surface coating.